Worldwide Copyrights reserved by Douglas Bryce . All rights reserved.
(Close to return to eBook page)
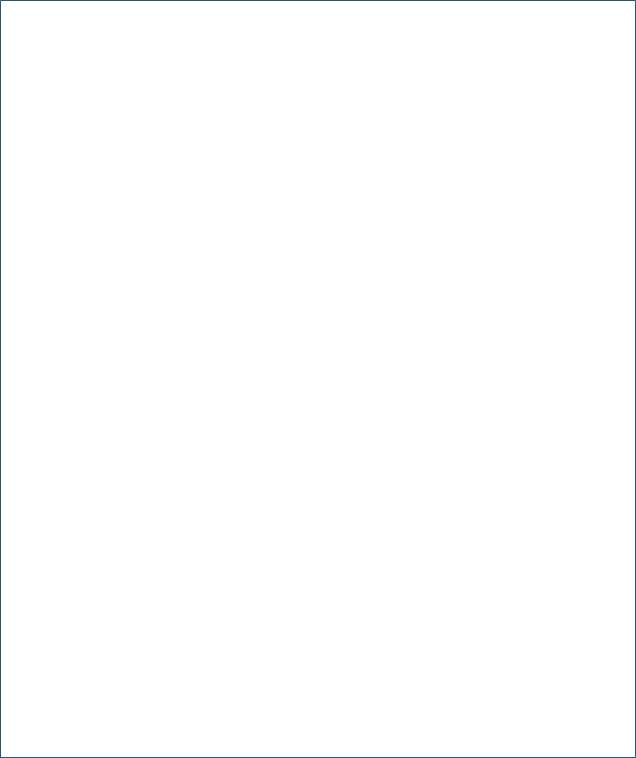
In an effort to become more competitive, and to reduce product development cycles, it has become necessary to address areas that may have been considered somewhat “sacred” in the past. One of these areas is that of using hardened tool steels for molds that produce “high volume” plastic parts. The cost of these molds has quadrupled in the last 20 years and average turn-around times have recently approached
4 to 5 months.
If an average product life cycle is now considered to be 12-18 months, it is evident that this product must be “rushed” to the marketplace as soon as it has been removed from the designer's possession. Turn-around times of 4 to 5 months jeopardize the potential sales impact of early market entry and present a notable financial exposure.
Likewise, the increase in tooling costs for these tool steel molds cannot be justified in the world's competitive arena that we now find ourselves. Greatly reduced mold costs are an absolute necessity to help ensure a place in this competitive environment.
A change from using tool steel in making molds to using aluminum alloys in making those same molds, whenever possible, will greatly enhance the market position and profit picture for any company that uses a commodity made of molded plastic. This will happen as a result of the reduction in TAT (by 50%) for the molds, and thus the product, and the reduction in part cost due to faster molding cycles and less tooling cost to be amortized. An added benefit is the higher level of quality available for parts molded in aluminum molds. Until now, these items were major gating factors in determining product costs and production schedules. With the utilization of aluminum alloy molds the impact of these items can be minimized to reasonable levels.
Next Chapter
Table Of Contents